Injection Molding (Plastic)
Latest Articles
In the process of mold making, the preparation of the electrode of the injection-molded tool is a basic premise for electro-galvanizing.
Shenzhen: The machinery industry has always been a traditional advantage industry in Shenzhen. At present, there are more than 12,000 mechanical production and operation companies in the city and nearly 850,000 employees. The annual output value of the mold industry in Shenzhen accounts for about 25% of the country's total. Stamping die and die casting die are known at home and abroad for their high precision, good quality and fast delivery. In 2007, the Shenzhen mold industry base covering an area of 1.6 million square meters has made breakthrough progress. The first-phase settled enterprises have started production in succession. A batch of digital versatile and specialized equipment manufacturers have developed well, the Shenzhen brand for mechanical equipment manufacturing has been launched in the market. Shenzhen is also the world's largest micro-motor production and export base, and the machinery industry has become the second pillar industry second only to the electronic information industry.
It is no exaggeration to say that plastic is the cornerstone of our society. The first step in the injection molding process is the clamping of the mold. This clamping device is a standard part of an injection machine. Mold, clamping device and injection device. The clip is a mold that melts the plastic injection, the injection mold is held under pressure, and the plastic is cooled.
If you want to be in the mass production section you want to make sure you get the right design for the first time. This is much more complicated than you think. What issues should be considered in injection molding production?
It is very important to choose a good mold manufacturer, because they not only can provide you with satisfactory molds, but also can make the after-sales easy. When the customer encounters a production problem, they can also consult these professional mold manufacturer, they will provide good advice to customers in many aspects such as design, production, etc., can save costs, improve efficiency, let customers sell products with better reputation and price during the use of customers. And that's a good business cycle what I've been looking forward to in the mold manufacturing industry.
The main advantage of injection molding is the ability to produce on a collective scale. Once the initial cost has been paid for at the injection molding production unit is extremely low.Consider some of the following things as you strive to make part of the production through injection molding.
Injection molding is a popular manufacturing method for many reasons. It has proven to be particularly valuable in consumer product development. Plastics The main component of many consumer products, injection molding is one of the best ways to make plastics. Let's take a quick look at the injection molding process.
Mold injection molding is a processing method that is used when mass producing certain complex parts. The specific principle refers to the plastic material that is heated and melted is injected into the mold cavity of a plastic mold by a high-pressure screw of an injection molding machine, and after being cooled and solidified, a plastic molded product is obtained.
The development of precision injection molds, precision injection molding was first produced in the 1970s. With the development of science and technology has been widely used, many industrial developed countries have reached a high level of research on precision injection molds. In recent years,China plastic injection mold has made certain achievements. Cheng Jun applied Pro/E to the design process of precision plastic molds. Taking the plastic mold of a certain type of mobile phone housing as a specific example, it was concluded that the 3D mold design of Pro/E is more efficient and intuitive than 2D design. Such advantages have important significance for the application of three-dimensional technology in precision plastic molds.
First point is size the crane to the MAX mould weight your largest press can support; you'll end up with that one mould that will be set in halves if you don't. Tie bar pullers for large machines. Standardize EVERYTHING! Water, power, valve gates, cores, air blow offs, weight blenders, mould mounting and ejection. I also recommend magnetic mould clamping. Think of material flow around the plant (raw material in and finished goods out the door) and machines (pallets, totes, boxes, racks). Consider keeping the smaller injection molding machines in the more land locked areas as a pallet can carry many different parts away but some 1000-2000t parts may only be 8 to a rack!! Data collection from the machines. Central drying and resin feeding.
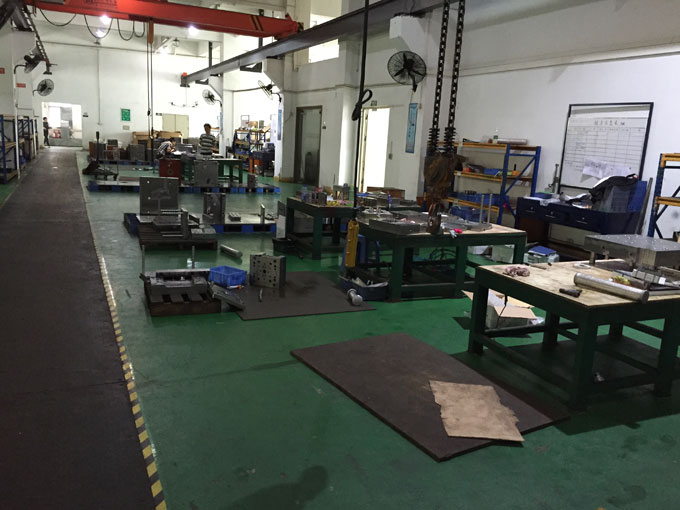
Extend robot strokes to allow for auto-packing of parts. Climate control so people won't leave and the moulds in the factory sweat all summer plus summer/winter process parameters stay the same. Tie water temp controllers into press. I'd put chiller and tower to the injection molding machines for best cooling choice for that resin/part. Stay with one brand of press and controller.
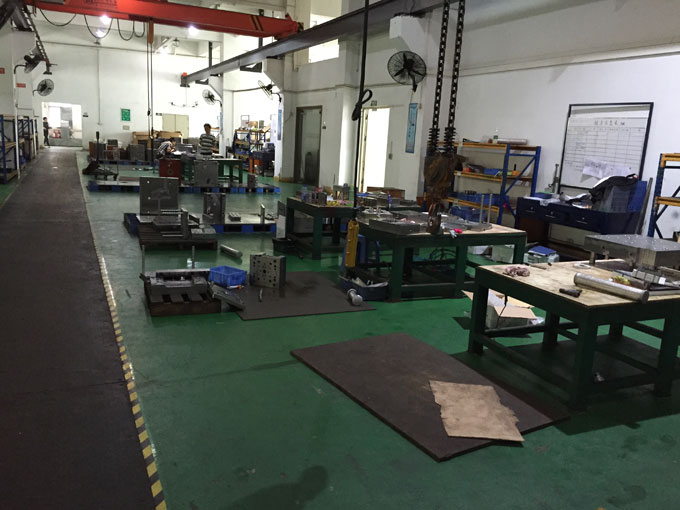
Extend robot strokes to allow for auto-packing of parts. Climate control so people won't leave and the moulds in the factory sweat all summer plus summer/winter process parameters stay the same. Tie water temp controllers into press. I'd put chiller and tower to the injection molding machines for best cooling choice for that resin/part. Stay with one brand of press and controller.
Rapid Temperature Cycling, (also referred to as Rapid Heat Cycle Molding or Vario-thermal Molding) will enable you to heat the surface of the injection mold to 200C.
The technology uses Saturated Steam to heat the injection mold and Tower Water to cool the injection mold. At the end of the cooling cycle Compressed Air is blown through the injection mold cooling channels to remove the water. Steam at up to 235C is then flowed through the cooling channels to heat the surface of the injection mold PRIOR to plastic injection, the steam is subsequently removed by Compressed Air followed by cooling water to remove the heat from the plastic.
The technology uses Saturated Steam to heat the injection mold and Tower Water to cool the injection mold. At the end of the cooling cycle Compressed Air is blown through the injection mold cooling channels to remove the water. Steam at up to 235C is then flowed through the cooling channels to heat the surface of the injection mold PRIOR to plastic injection, the steam is subsequently removed by Compressed Air followed by cooling water to remove the heat from the plastic.
Labor: A whole line would require only two people (the whole line is compounded by compression molding machine, folding, slitting and lining (EVA) machines).
Maintenance: The compression molding and other lines machines have a different but, in my opinion, easier maintenance. The mold centenarian is also easier due to you deal with every cavity separately, no frame, no plates.
Quality: The compression molding machines has a per unit quality inspection on line, discarding any off specs closure from the production line - That is not possible using injection molding process - Also the closures has minimum stress compared with injection molding.
Raw materials: the common resin is PP, it's better to use a lower melt flow index but the range suitable for this process is wider that the required for injection molding.
Productivity: At the end of the line you will have a bigger and better production with compression molding compared with similar cavitation molds using injection molding. A usual rotary machine may have 64 cavities and its production may be as high as 60 MM caps/month.
Costs: Also at the end of the month your production costs will be lower using compression molding compared with Injection.
Market: Most Soft drinks producers and water bottlers around the world know and trust in compression molded closures.
Maintenance: The compression molding and other lines machines have a different but, in my opinion, easier maintenance. The mold centenarian is also easier due to you deal with every cavity separately, no frame, no plates.
Quality: The compression molding machines has a per unit quality inspection on line, discarding any off specs closure from the production line - That is not possible using injection molding process - Also the closures has minimum stress compared with injection molding.
Raw materials: the common resin is PP, it's better to use a lower melt flow index but the range suitable for this process is wider that the required for injection molding.
Productivity: At the end of the line you will have a bigger and better production with compression molding compared with similar cavitation molds using injection molding. A usual rotary machine may have 64 cavities and its production may be as high as 60 MM caps/month.
Costs: Also at the end of the month your production costs will be lower using compression molding compared with Injection.
Market: Most Soft drinks producers and water bottlers around the world know and trust in compression molded closures.
Category
Featured Articles
How to Choose a Good Chinese Injection ...
It is very important to choose a good mold manufacturer, because they not only can provide you with satisfactory molds, but also ...
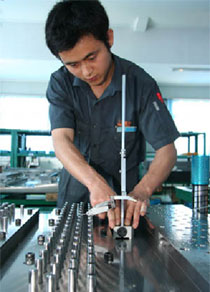
Precision Injection Mold Technology in ...
The development of precision injection molds, precision injection molding was first produced in the 1970s. With the development ...
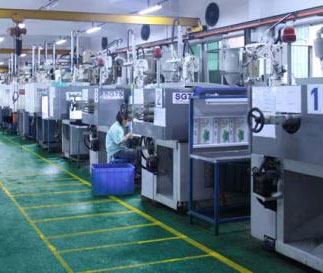
Plastic Injection Molding Process ...
The propositions behind injection molding process simulation are very basic. First, that although our plastic materials and ...
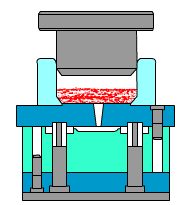
Visit injection molding factory in ...
Not being in the injection molding industry, I was looking for tips on how to judge a company or factory on their capability or ...
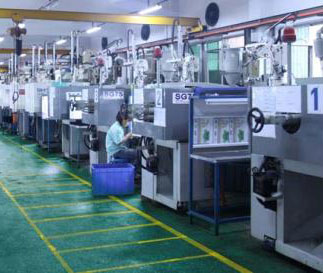
Injection Mold Cooling Design
The design of the injection mold cooling system is very important. The cooling time takes up 70% to 80% of injection molding ...
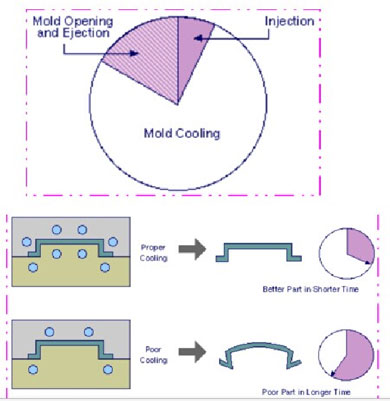